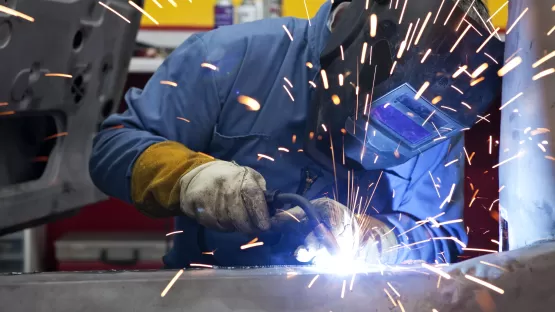
Quel est l’impact de la pureté du gaz de soudage et coupage ?
En fonction du métal à souder et du procédé utilisé, le degré de pureté du gaz influencera la vitesse de soudage, la finition du cordon et surtout la porosité. Les impacts de toute sorte d'impureté créent un certain nombre de défauts et de problèmes.
Le gaz de soudage principalement utilisé - en procédé à arc électrique, plasma, laser, TIG, MIG et MAG - est l’Argon ; c’est le gaz de base utilisé en fabrication métallique.
Il convient de préciser que les niveaux d’impuretés de l’Argon sont à considérer en fonction du métal de base et du procédé. En ce sens, l’azote est extrêmement dommageable pour l’acier mais peut être relativement neutre pour les aciers inoxydables austénitiques, voire favorablement utilisé pour les aciers duplex par exemple. Les niveaux d’impuretés acceptables sont donnés dans les normes de soudage, mais il convient de les considérer en rapport avec l’application finale.
L’oxygène (air) et l’azote sont deux des impuretés principales usuelles de l’Argon, ayant des effets néfastes lors de l’utilisation du gaz de soudage pour la plupart des procédés. Ainsi, Air Liquide vous éclaire sur les niveaux de pureté des gaz (purs ou mélanges) utilisés en industrie pour le soudage des principaux matériaux.
L’acier carbone
L’acier carbone est un matériau qui ne supporte pas l’azote. En effet, l’azote atomique est soluble dans l’acier liquide. Cependant, il ne l’est pas dans l’acier solide. Ainsi, si de l’azote est présent dans l’acier carbone, il créera des bulles lors de la solidification, et donc des porosités, ce qui a un impact direct sur la qualité des pièces produites.
Les conditions de présence des principaux polluants sont déterminées dans la norme EN ISO 14 175. Elle impose moins de 1000 ppm d’azote. En prévision d’applications plus exigeantes, Air Liquide considère toutefois que cette limite supérieure peut affecter négativement les propriétés mécaniques. En effet, les gaz purs ou mélanges de gaz Air Liquide de la gamme ARCALTM contiennent pour leur grande majorité moins de 200 ppm d’azote pour obtenir de meilleurs résultats.
L’oxygène (autre constituant de l’air) peut être utilisé à faible concentration lors du soudage des aciers dans l’industrie. Il convient toutefois de bien maîtriser sa teneur pour optimiser la maniabilité en fonction de la vitesse d’avance par exemple.
L’eau (H2O) se dissocie au niveau de l’arc sous forme d’hydrogène et d’oxygène. L’hydrogène en particulier est susceptible de passer dans l’acier. Cela a un impact direct sur la qualité puisqu’il fragilise l’acier carbone par fissuration à froid. Pour une application en soudage, entre 40 et 120 ppm d’H2O sont tolérés selon la norme EN ISO 14 175. Air Liquide et sa gamme de gaz pour soudage ARCALTM retiennent usuellement 40 ppm comme limite haute.
L’acier inoxydable austénitique
Pour le soudage de pièces en acier inoxydable austénitique, l’azote ou l’hydrogène ne sont pas gênants en faible teneur. Ils peuvent même contribuer favorablement à la métallurgie (N2) dans certains cas, ou améliorer les paramètres opératoires et l’aspect de cordon (H2).
En soudage MAG des inox, un élément oxydant est indispensable pour la stabilisation de l’arc. Toutefois, l’excès de CO2 peut provoquer des précipités de carbure de chrome dans la soudure, ce qui affectera la résistance à la corrosion de l’assemblage. Ainsi, généralement, pour souder l’acier inoxydable, il ne faut pas dépasser 3% de CO2. Un excès d’oxygène aura le même effet, plus oxydant, donc plus agressif jusqu’au phénomène de rochage par exemple. Ainsi, on ne dépassera pas 2 à 3% d’oxygène dans l’argon.
Le saviez-vous ? Les différents aciers permettent la production de diverses pièces qui seront utiles dans le marché mondial de l’analyse et du médical, où l’inox est apprécié car il limite le développement des micro organismes, ainsi que dans l’industrie chimique avec des aciers inoxydables ou des duplex, en fonction des températures et du type de corrosion rencontrés.
L’aluminium
L’aluminium ne supporte ni l’azote à relative forte teneur, ni l’hydrogène, ni l’H2O (eau). Ainsi, pour éviter les porosités, des gaz de haute pureté doivent être considérés.
L’aluminium et ses alliages sont, de manière globale, soudés sous atmosphère inerte telles que l’argon et l’argon / hélium, voir hélium pur dans certains cas. Une attention particulière est à prendre à la préparation de l’état de surface avant soudage: l’alumine présente en surface des pièces peut contenir suffisamment d’humidité pour engendrer des porosités même avec un gaz contenant très peu d’impuretés.
Air Liquide, un leader international des gaz industriels, peut vous conseiller par rapport au degré de pureté nécessaire pour vos industries selon vos besoins. La plupart des gaz Air Liquide, en particulier de la gamme ARCALTM , va au-delà des attentes de la norme.
Découvrez nos solutions
Avez-vous des questions sur l’impact de la pureté du gaz ? Veuillez remplir notre formulaire de contact.
Nos experts vous répondront dans les 24 heures.En savoir plus
Soudage industriel, techniques et procédés
Défauts de soudage (Matériel de soudage, matériel de soudure)
Mélanges de gaz pour le soudage par fusion
Le procédé de soudage MIG/MAG (GMAW)
Quelle est la différence entre les procédés de soudage MIG et MAG
Température de fusion du métal
Questions fréquentes
Comment souder l'acier galvanisé ?
Comment souder l'acier inoxydable ?
Comment choisir le gaz à utiliser en MIG ou MAG ?
Comment choisir le gaz à utiliser en TIG ou Plasma ?
Comment éviter les surconsommations de gaz de soudage ?
Utiliser un fil fourré, pourquoi ?
Comment régler le débit de gaz en soudage ?
Quelle est la différence entre brasage et soudage ?
Quels sont les défauts de soudage les plus communs ?
Quel est l'impact de la pureté du gaz de soudage et coupage ?